Jump to:
The Importance of Quality Industrial Cleaning | Necessary Resources | Benefits | Products Needed | Steps To Equipment Cleaning
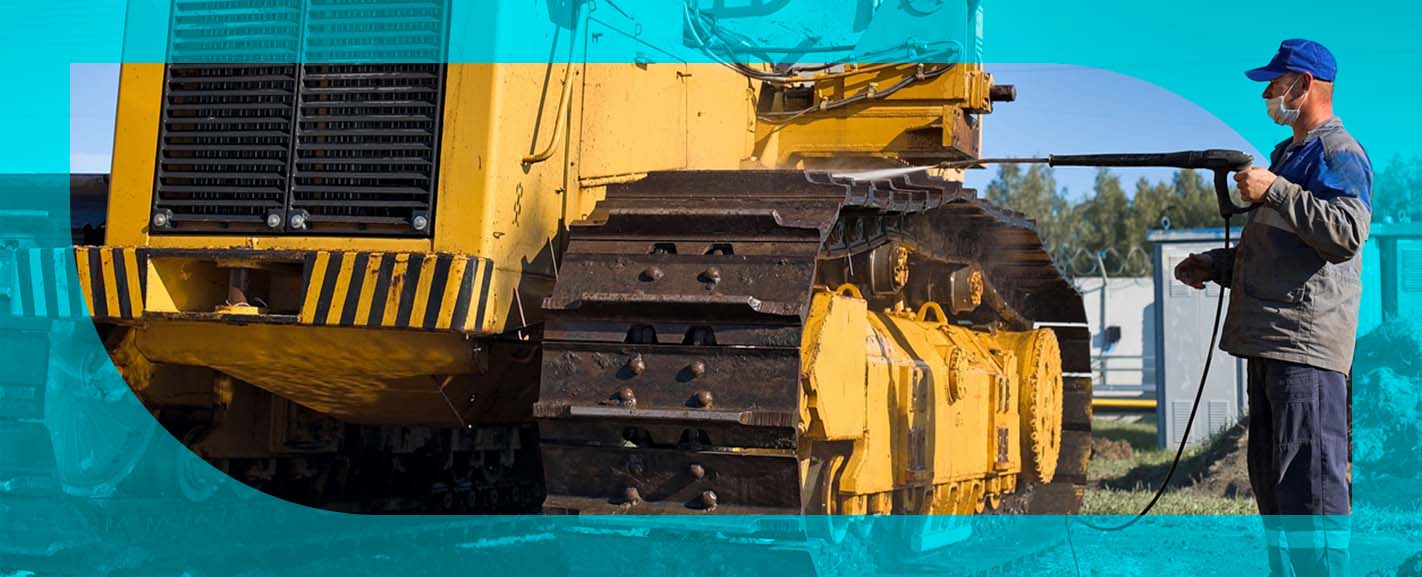
Cleaning and degreasing equipment is important in construction processes. Well-maintained equipment operates efficiently and lasts longer, saving owners and operators time and money.
Equipment cleaning involves more than rinsing machinery or wiping it with soap and water. It requires specific detergents and specialized cleaning equipment. With the proper resources, construction site workers and managers can ensure equipment remains efficient and operational for as long as possible.
The Importance of Quality Industrial Equipment Cleaning
Cleaning heavy equipment is necessary for all construction equipment. Many choose to pressure wash their equipment, which removes grime, grease and mud quickly and helps your equipment last longer, protecting your investment. To clean equipment effectively, equipment owners and operators need special equipment, techniques and safety factors.
There are many reasons to wash heavy equipment. Successful construction companies, equipment rental yards and heavy equipment dealerships significantly benefit from keeping their expensive machinery clean and in top-notch condition.
Equipment efficiency and long service life are critical to making sure machines are always operational when needed. A nonworking machine is a nonpaying machine, and cleaning equipment helps machines remain operational to reduce unscheduled downtime.
Learn More About Heavy Equipment Cleaning Solutions
What Resources Are Necessary to Clean Industrial Equipment Effectively?
Heavy equipment cleaning requires specialized equipment such as water cannons or pressure washers. It also involves specific techniques that make the best use of cleaning time and materials. Workers must consider safety factors when performing heavy equipment cleaning.
Heavy construction equipment like excavators, loaders and gravel trucks are large, complicated machines that can present hazards to operators and those who clean them regularly. Implementing safety guidelines protects operators and cleaning staff from potential accidents.
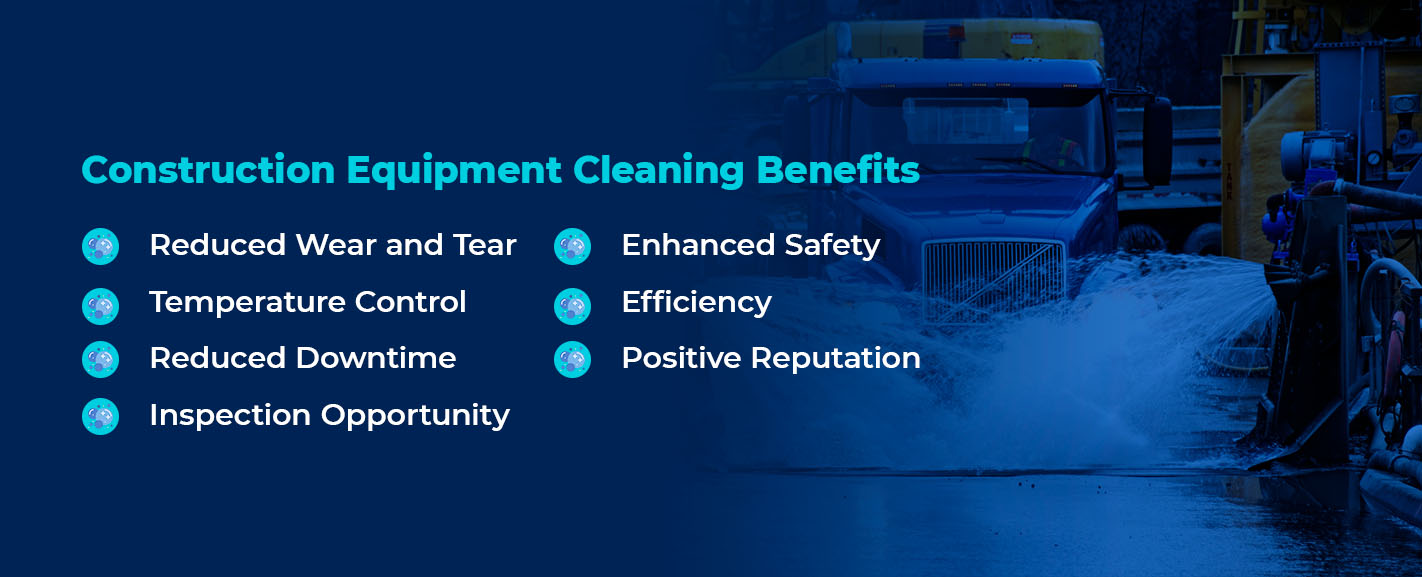
Construction Equipment Cleaning Benefits
Keeping heavy machinery clean is professional and should be part of any industrial company’s overall routine and preventive maintenance program. Equipment owners and operators should make cleaning equipment a top priority because it offers the following benefits:
Reduced Wear and Tear
Regular cleaning is an essential part of preventive maintenance. Grime and dirt are abrasive and cause friction in machines, but regular cleaning reduces the strain on moving and fixed parts. Clean machines last much longer than dirty machines, and regular washing makes machines easier to clean than if they gradually collect dirt and grime.
Temperature Control
Clean machines keep cooler than mud-caked and grease-soaked equipment. Although regulated heat is a necessary operating condition with heavy machinery, excessive heat is a killer. Keeping equipment cool can extend a piece of equipment’s life span and prevent it from malfunctioning mid-operation. This positively affects other machines and workers in the production chain.
Reduced Downtime
Keeping construction equipment clean reduces machine downtime. Dirty conditions can cause part failures and breakages, leading to lost time and costly repairs. Regular cleaning removes foreign matter like rocks and branches in tracks. Removing heavy, dried sludge from surfaces reduces excessive weight on booms and buckets.
Inspection Opportunity
Cleaning machines is a great opportunity to inspect for potential problems. Cleaning exposes metal fatigue cracks, oxidization and rusting. Worn or leaking fittings are also obvious when machinery is clean. This allows mechanics to get on top of developing problems before they become serious issues.
Enhanced Safety
Regularly cleaned construction machinery enhances safety. Poorly kept equipment is dangerous to the operator, work crew and others in the machine’s line of fire. Cleaning prevents contaminant buildup around hydraulic and electrical systems, which also prevents potential damage such as a serious blow-out of high-pressure oil or dangerous voltage.
Efficiency
Mechanics are much more efficient when they work on clean machines. Cleaning dislodges foreign debris that’s heavy, volatile or slippery and that can cause falls. Falls are one of the most common construction site risks, so it’s important to prevent them. Effective washing removes objects and buildups that can cause injury from slips and falls, and it prevents workers from being pinched in points that trap kinetic energy. Clean and safe surfaces significantly reduce ergonomic accidents.
Positive Reputation
Clean equipment makes a loud and positive statement. Clients, investors and future customers notice when companies keep their equipment clean, and this increases their trust. Clean and orderly equipment also increases ownership pride. This applies to business owners, supervisors, machine operators and service people. Operators and maintenance technicians take more care when running clean and well-kept equipment.
Products Needed to Wash Heavy Equipment Effectively
Properly washing heavy equipment requires technical knowledge to remove dirt and grease buildup effectively. Using an efficient step-by-step cleaning procedure saves time and energy, and implementing safety procedures keeps washing technicians safe. To develop an efficient and safe cleaning procedure, you need certain products and equipment.
Equipment cleaning products vary in cost and ease of use, but they all have their purpose in ensuring a proper, safe and efficient job. The main products professional machinery cleaners employ are the following:
Personal Protection Equipment
Personal protection equipment is the first product to consider when starting a machinery washing job. Safety is paramount at every construction site, shop and yard. It’s crucial to take personal safety seriously. Construction machinery and designated cleaning equipment are hazardous. Workers need the following personal protective equipment:
- Full-length coveralls: Coveralls protect the entire torso, arms and legs. Today, practically all construction workers wear high-visibility outerwear such as disposable or reusable coveralls. Specialized rainwear such as machinery overalls or two-piece jackets and pants are suitable for this purpose. Insulated protection is important if using hot water washing.
- Protective footwear: Protective footwear is vital. The best footwear is commercial rubber boots with anti-skid soles and toe protection. Upper closure is also important. This prevents hot water from filling up boots.
- Face and eye protection: Wrap-around eyewear or full-face shields protect workers and cleaners from splashes, dirt, chemical burns and eye contamination.
- Gloves: Gloves are mandatory. Workers need to hand-remove chunks of clay and all sizes of stones from machines, and gloves protect them from sharp edges on machine parts. Some workers wear leather gloves when washing, but most find rubber or latex protects hands best.
Pressure Washing Equipment
Pressure washers are mandatory products to use when cleaning construction equipment. A pressure washer is the best tool for removing dirt, grease and grime. Pressure washers force concentrated water streams into tight places like hinges and seams that are impossible to reach with hand brushing.
High-pressure washing equipment consists of pressure washers and high-pressure water cannons. Both perform similar functions but at different scales. Pressure washers are small-scale devices with a limited amount of water flow. They have high pressures between 2,500 and 3,000 pounds per square inch (PSI) but their capacity is limited to about 5-10 gallons per minute (GPM). Pressure washers are equipped with small diameter hoses, usually ½ inch.
Water cannons are much larger than pressure washers. They have lower pressure rates, but water cannons flow at 20-150 GPM or more. That’s 4-15 times the rate of a small-scale pressure washer. Water cannons use fire-type hoses with 1 to 1-½-inch diameters and have adjustable nozzles.
Water cannons are typically found on commercial equipment washing stations that have dedicated closed-loop wash racks. They expel large volumes of water that’s captured, cleaned and recycled. Both types of high-pressure washers are capable of using hot and cold water. Often, pressure washers and cannons operate in tandem with cannons doing the big removal and overall final rinse. Pressure washers perform fine detailing.
Heavy Equipment Wash Pads and Racks
There’s no substitute for using a professionally designed and built wash pad, which is also known as a wash rack. Many jurisdictions regulate wash locations to ensure they comply with environmental compliance. Laws prohibit contaminated construction equipment washings from entering open surfaces and groundwater reservoirs.
Non-compliance with laws can result in heavy fines and personal jail time, not to mention being environmentally irresponsible. In addition, containing contaminated wash water can also protect the property owner or renter from a very expensive soil and groundwater cleanup.
Properly constructed wash pads and racks are built with water containment and recycling systems. Wash pads should be self-contained and enclosed to prevent wash water and all its pollutants from escaping into the outer environment. This knocks dirt, grease and other contaminants free so they can collect inside sumps.
Closed-loop wash operations or wash racks capture and recycle excess water in a contained system, filtering it back to workable gray water where it’s continually reused.
ESD Waste2Water’s Washing System
Wash racks and pads are available in many sizes depending on the company’s needs. Water storage tanks vary depending on how frequently a company uses a wash pad and how large the serviced equipment is. Hot and cold temperatures are usually available for the washing equipment, and pressure rates are controllable. Additionally, some wash racks are fixed and stationary while others are mobile so workers can transport them from site to site.
Solid waste management is an important wash pad function. Like water, solid wastes need proper containing and disposal. While a closed-loop system recycles water, it collects, dries and moves solid waste to a safe disposal site. Some wash racks are designed with above-ground solid management systems (SMS) while others depend on underground sumps and mud-drying pads.
Check Out ESD Waste2Water’s Washing System:
Call Us At 1-800-277-3279 Today To Get a Quote!
Cleaning Detergents, Surfactants and Water Temperature
Heavy equipment requires more than water to dislodge dirt and grease. Every equipment wash system employs a type of degreasing solution. The best type of degreasing solution depends on the type of equipment you need to clean and the site conditions it operates under.
The most common contaminants in heavy equipment are organic and inorganic compounds. Organics include hydrocarbons like lubrication grease and fuel residue. They also include vegetation contamination from brush clearing and even insect and bird waste. Inorganics generally refer to mineral compounds like sand, gravel and dust.
Another contaminant category is a mixture of organic and inorganic compounds. The most common mixture is soil, which occurs virtually everywhere. Soil is made of decomposing organics and static inorganic compounds. Often, the soil itself is polluted. Soil can also be one of the hardest materials to clean. This is because contaminants bond to machinery surfaces. Detergents are important because they can remove organic and inorganic compounds from equipment.
Many people call detergents soap, but they differ from soap. Soap refers to cleaning products made from natural materials like lye and animal fat. Most cleaning agents today are synthetic products carefully designed with specific chemical properties.
Heavy equipment washing detergents act as surfactants or surface active agents. When dissolved in water or other solvents, surfactants work at the boundary between the liquid and solid to change the interface properties. Water mixed with detergent breaks the bond between dirt and host objects. Water has a limited effect on its own.
Chemically speaking, synthetic detergent surfactants work at the molecular level and form a long chain that attaches one end to a hydrophobe like dirt or grease. The other end is attracted to water or the hydrophile solvent. This causes the surfactant to surround the contaminant and dislodge it from its bonded surface, like dirt coming off machinery parts.
Chelating agents are often added to equipment washing detergent. These also work at the molecular level, but they attack minerals in the water to soften them and stop hard water from blocking surfactant efficiency. Other additives in detergents like color, foaming agents and perfume don’t help cleaning power. They simply make the product look and smell more attractive.
Wash water temperature is also misunderstood. Cold water washing is highly effective when used with the right surfactant. Hot water warms the machinery surface making large chunks of debris break off easier, but the temperature is not particularly sensitive at the molecular level where the real cleaning action is.
Cleaning Construction Equipment Quickly and Easily
There is a distinct process to clean equipment quickly and easily. Priority steps speed things up and prevent workers from doing the same task twice. Every equipment cleaner has their individual preferences, but the proper washing procedure goes this way:
- Workers start by assembling all washing products and placing machinery in a contained wash rack with a closed-loop system. They also ensure they wear all necessary PPE.
- Next, workers manually pry large dry chunks of material from the chassis and undercarriage with a spade and steel bar. This is much safer than immediately attacking the machine with high pressure.
- Workers also collect and dispose of debris chunks. This prevents a tripping hazard while navigating around the machine. It also stops dried debris from being liquefied, making it more difficult to handle.
- Next, the entire machine is sprayed with a water cannon to remove large debris pieces that couldn’t be dislodged by hand. Warm or hot water from a hot water pressure washer is often used in this early stage which is prior to adding detergent.
- The next step is to manually remove grease accumulations by pulling chunks off or wiping them with cloths. By now grease will have softened by water force and temperature.
- Detergent is applied sparingly, with special attention to visible contamination. This includes engine compartments and especially radiators.
- Cleaning solvents are allowed to sit for 15 minutes to ½ an hour. This gives time for surfactant molecular action to dislodge all bonding chemically.
- Water cannon force starts again. It begins at the top of the machine and orderly flows toward the ground, letting gravity pull contaminants and wastewater to the wash pad floor.
- Workers detail tight places, seams and joints following the overall cannon rinsing. Here, smaller pressure washers might be used as well as hand scrubbing for detailing the equipment.
- Next, workers clean hoses and rubber tires with a suitable surfactant, and they clean and polish glass surfaces.
- The following step is to vacuum and hand-wipe cab interiors. High-pressure washing should never be used inside cabs or around controls.
- Once the machine is generally cleaned, it’s allowed to air dry. Sometimes, compressed air is used to hasten the process.
- When a machine is dry, workers remove it from the wash rack and send it to its next operation, which might be maintenance, repair or back into stock for sale or rent.
- Finally, workers inspect all parts of the wash pad. They clean mud off of the wash pad surface, dispose of solid waste and top the gray water levels. They also perform a perimeter check to ensure that no contaminants escape.
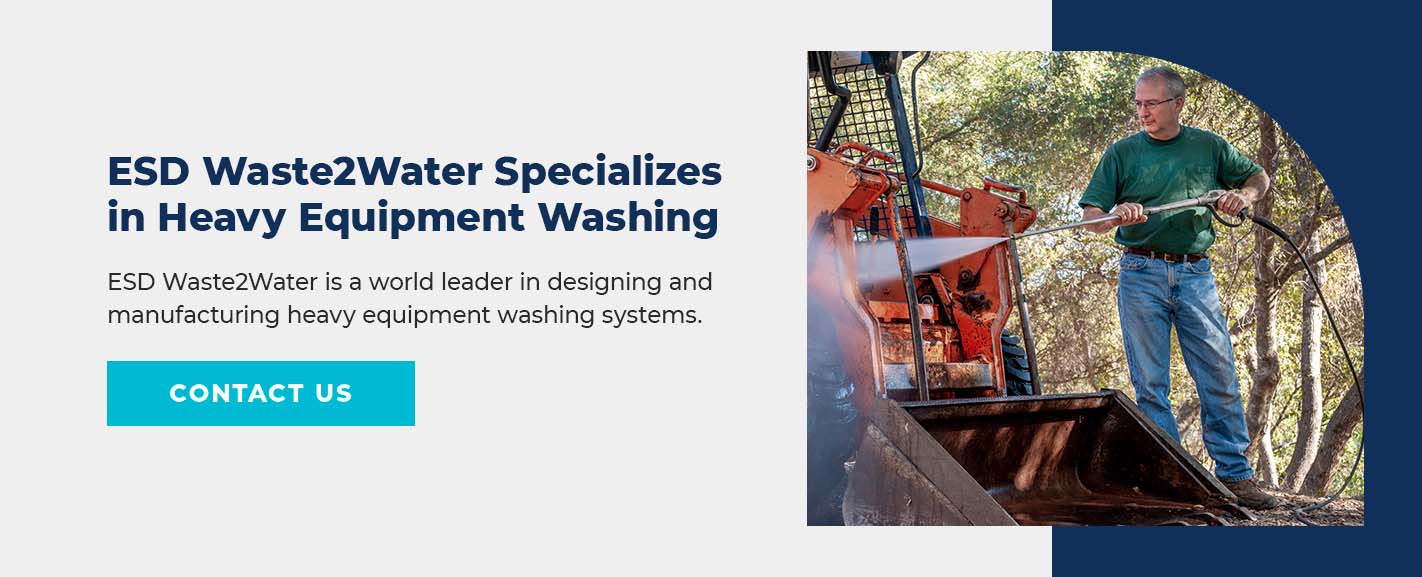
ESD Waste2Water Specializes in Heavy Equipment Washing
Correctly cleaning heavy industrial and construction equipment is crucial. Proper cleaning procedures ensure equipment operates effectively and efficiently, and it helps equipment last as long as possible, saving equipment owners money. Keeping equipment clean also helps operators remain safe on job sites by preventing slips, falls and cuts.
ESD Waste2Water is a world leader in designing and manufacturing heavy equipment washing systems. We’re located in Central Florida and supply top-quality closed-loop washing systems to many countries. We also specialize in solid management systems and incorporate the two, making the most efficient and effective construction equipment washing process possible.
ESD Waste2Water provides installation, service and training with all our products. We supply unsurpassed cleaning and wastewater control systems. Our high-technology lines include everything you need to wash heavy equipment effectively and efficiently.
Contact ESD Waste2Water to learn more about our manufactured products or start a custom-designed solution for washing your construction equipment.